Universal Plastics offers a full complement of secondary services to our customers so that we can meet all of your needs, end to end. Our secondary service capabilities include class A high gloss paint services (automotive quality), complex assemblies, drape forming, RFI/EMI shielding, screen printing, warehousing, etc.
For more information on our secondary services or to discuss your needs, please contact us.
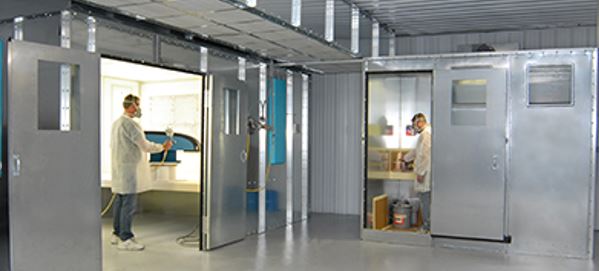
High Gloss Painting (Class A, automotive quality)
Universal Plastics offers class A automotive quality high gloss painting services, with six state-of-the-art paint booths (including two high gloss paint booths) capable of handling part sizes up to 11’x11’x3′. We also do QC inspections with CMM Color conformance with a Datacolor 600. Our painting service can match colors exactly to your specifications and will provide your products with the highest quality finish. Universal Plastics’ in-house painting facility can provide any color or finish clients require – including EMI/RFI shielding and water-borne paint. Our in-house finishing means that we assume responsibility for products from design to finish. Universal Plastics also offers screen-printing (even on textured surfaces), and PAD-printing as well as hot-stamping in single or multiple colors.
Anticipating increasing customer demand for Universal Plastics’ high-gloss painted parts, we completed construction of three new state-of-the-art paint booths. We have also created a dust-free environment to ensure the highest quality of our painted finishes. Shown is an image of a DNA Sequencer manufactured and wet painted by Universal Plastics.
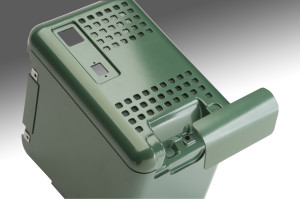
Complex Assemblies

Drape Forming
Universal Plastics’ drape forming capabilities enable us to design and form optically clear enclosures of a wide range of shapes and sizes, based on your specific needs. The image here is a test chamber manufactured and drape formed by Universal Plastics.
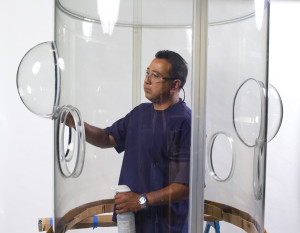
Secondary & Finishing Capabilities at Universal Plastics:
Universal Plastics is the largest precision heavy gauge custom thermoformer in the Northeastern US with an asset base of 22 pressure formers, 14 vacuum formers and 26 5-axis trimming machines, supplying our customers with vacuum forming, pressure forming, including twin sheet forming and complex assemblies, with part sizes up to 12’ x 9’. In addition, we offer in-house tooling, an experienced engineering staff, and a full complement of secondary/finishing services, including our new state of the art paint booths which can produce automotive quality finishes. With a range of rotary formers, rapid manufacturing processes, and a global supply chain, we can produce thermoformed parts at the most competitive prices.
In addition to custom thermoforming, Universal Plastics also offers injection molding (including gas assist and structural foam molding) and custom blow molding. We would be glad to talk with you about the optimal process for your needs.
Contact us to discuss how we can meet your custom plastic part needs.