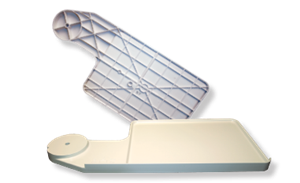
Gas Assist Injection Molding Process Overview:
Gas assist injection molding is a process that produces large plastic parts with complex designs and superb cosmetic surface finishes. The process is especially ideal for large handles, equipment covers, doors, bezels, cabinets and skins. By injecting a controlled stream of gas (nitrogen or carbon dioxide) into the mold, thick walls are created with hollow sections that save on material, shorten cycle time, and reduce the pressure required to mold the large plastic parts with complex designs and attractive surface finishes. All of these benefits are realized without any detriment to the structural integrity of the molded component. For more on how we can help to design or transition your parts to gas assist injection molding, contact us.
Applications:
Universal Plastics’ comprehensive gas assist injection molding capabilities provide innovative solutions to exceed the limitations of traditional injection molding. Applications for gas assist injection molding include metal to plastic conversion, consolidation of components, and weight reduction of thick-walled sections. Although gas assisted injection molding offers many advantages including less material usage, a desirable surface finish, and lower tooling costs, many customers are not familiar with the process. We can bridge that knowledge gap and advise customers whether their design could be better served by gas assist injection molding in place of traditional or structural foam injection molding.
Our customer base includes OEM producers of retail kiosks that provide automated services, laboratory and diagnostic equipment designers, medical equipment manufacturers, and large office equipment companies. In addition to gas assisted molding, traditional injection molding and structural foam molding are available.
Our full range of secondary and finishing services including painting, inserting, printing, assembly and packaging provide customers with a single source for turnkey injection molded parts.
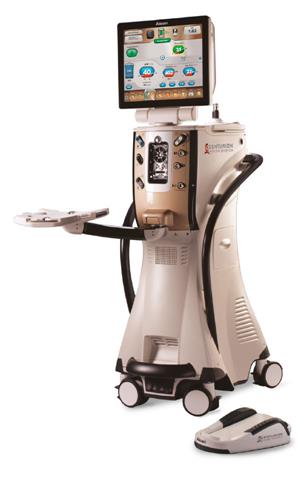
Gas Assist Injection Molding Capabilities at Universal Plastics:
Universal Plastics offers both internal and external gas assist injection molding which allows us to create a myriad of complex part geometries not previously achievable by injection molding. Instead of requiring multiple parts that must later be assembled, supports and stand-offs are easily integrated into a single mold without the need for complex coring. Our several injection molding machines are capable of producing parts from 10″ to 80″ long and from 10″ to 70″ wide.
Rapid Heat Rapid Cool Technology with Gas Assist:
What is Rapid Heat Rapid Cool with Gas Assist? It is a process where we heat the tool up while injection molding and cool it down rapidly during cooling while concurrently packing out the part for no sink utilizing a nitrogen gas. Our Rapid Heat Rapid Cool with Gas Assist process achieves a Class A type surface without sink. Adding the Heat and Cool portion to the molding of the part with Gas Assist can take your designs to the next level and eliminate paint! We can also achieve this with glass filled materials. There are many methods to achieve the heating and cooling of the tool. Some of those methods are: hot oil, steam, high-pressure hot water and induction.
Based on the volume of your application we can help to determine which method is right for your situation. Contact us to discuss.
Gas Assist Injection Molding:
Universal Plastics started its gas assist injection molding process development in 1985, when we founded the Nitrojection Technology. James Hendry, considered father of gas-assist injection molding, worked at Universal Plastics. To date, we have commercialized over 500 different parts with this technology and are the only supplier with a UL Yellow card for Gas Assist (UL Yellow Card # E76823(N)).
The gas assist injection molding process is a low pressure, conventional injection molding process that forces a short shot of material to fill a mold by using pressurized nitrogen gas to displace the material in pre-destined thick area while forming hollow sections in the part.
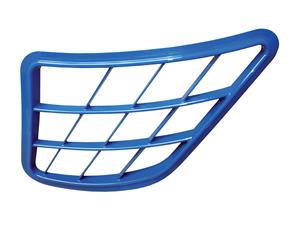
Internal Gas Assist Injection Molding:
The pressurized gas pushes the molten resin tight against the cavity walls until the part solidifies, and the constant, evenly transmitted gas pressure keeps the part from shrinking while also reducing surface blemishes, sink marks, and internal stresses. This process is ideal for holding tight dimensions and complex curvatures over long distances.
External Gas Assist Injection Molding:
In external gas assist injection molding the molten resin is introduced into the mold, but the gas is injected in a micro-thin layer between the back surface of the part and the mold core, thereby forcing the front surface of the part against the opposite side of the mold cavity. As the resin cools the pressurized gas guarantees the front side of the part precisely replicates the surface of the mold.
On the left, classic injection molded (CIM) parts show evidence of resin shrinkage on the front side areas of the rib/wall junction. For external gas assist injection molding (EGAIM) gas packing on the reverse side of the part prevents front side shrinkage.
This process is best for high profile and large surface area plastic parts, especially those requiring detailed textures and superior surface aesthetics. Warp and sink marks are eliminated because the gas packs out the resin as it solidifies. As with internal gas assist, support ribs and bosses can be molded into the part yielding similar dimensional stability and tight tolerances. Molding pressures are also likewise reduced generating less residual stress on parts and wear on molds.
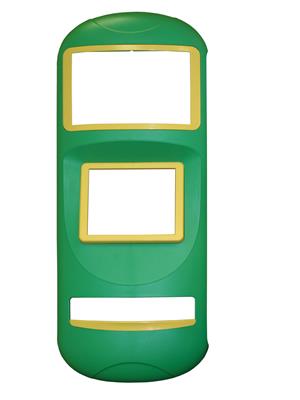
Cost Considerations:
Along with potential reduction of part count, additional savings are achieved through use of the gas assist processes. Since they typically require one-third the clamping force of conventional injection molding the same part size may be run with a lower tonnage press, not only keeping part costs under control but also introducing less residual stress into the part to further aid dimensional stability. Reduced in-mold pressure subjects the mold to less wear and tear, allowing the use of less expensive aluminum tooling. Parts also weigh considerably less, which results in reduced freight expense and improved material handling efficiencies.
Design Benefits:
This technology offers many design and performance advantages over other large part molding processes. Multiple parts with differing wall thickness and complex designs can be molded as a single part with tighter tolerances. Support ribs and bosses can be molded into the part itself, and the gas channels can be directed to eliminate evidence of these support features on the customer facing side of the parts. For these reasons parts exhibit improved dimensional stability and higher quality surface cosmetics, while requiring minimal or no secondary operations.
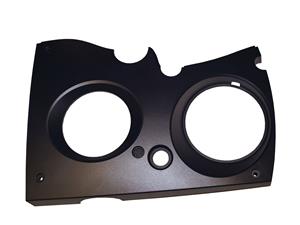
Converting Existing Parts to Gas Assist:
Gas assist injection molding is an attractive option for producing a better quality alternative to existing large metal parts. Customers achieve tremendous performance benefits by eliminating expensive, heavy, corrosion-prone parts such as covers, enclosures, access doors, and panels. Another attractive conversion opportunity is the replacement of existing thermoformed, vacuum formed, or pressure formed parts.
Formed parts require labor-intensive, expensive secondary operations and the cost savings associated with gas assist justifies the investment in tooling to convert to gas assist injection molding once production quantities reach modest levels. Part features such as support ribs, bosses, and windows can be incorporated into the mold of a gas assist part and the costs of gluing, bonding, trimming and machining normally necessary for thermoforming can be eliminated.
Through early involvement in the engineering and design process, Universal Plastics can provide you with a competitive advantage through use of gas assist plastic injection molding. Universal Plastics also offers custom thermoforming, blow molding, traditional injection molding and custom blow molding, so we can work with you to understand the best manufacturing process for you based on your part volume, design and other needs. We pride ourselves on our ability to offer unbiased, process-agnostic advice and multiple production processes for high mix / low volumes, low mix / high volumes and the breadth in between. Contact us today to learn more.
Secondary & Finishing Capabilities at Universal Plastics:
Universal Plastics has a long history of expertise in manufacturing thermoformed plastic panels. Contact us today to discuss your ideas.
Universal Plastics is the largest precision heavy gauge custom thermoformer in the Northeastern US with an asset base of 22 pressure formers, 14 vacuum formers and 26 5-axis trimming machines, supplying our customers with vacuum forming, pressure forming, including twin sheet forming and complex assemblies, with part sizes up to 12’ x 9’. In addition, we offer in-house tooling and a full complement of secondary/finishing services, including our new state of the art paint booths which can produce automotive quality finishes. With a range of rotary formers, rapid manufacturing processes, and a global supply chain, we can produce thermoformed plastic panels at the most competitive prices.
In addition to custom thermoforming, Universal Plastics also offers injection molding (including gas assist and structural foam molding) and custom blow molding. We would be glad to talk with you about the optimal process for your needs.
When is Gas Assisted Injection Molding Used?
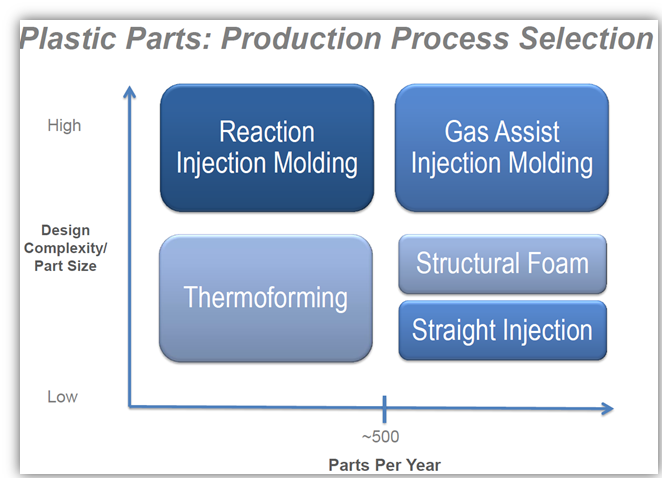
Benefits of Gas Assist Injection Molding Vs. Other Production Processes:
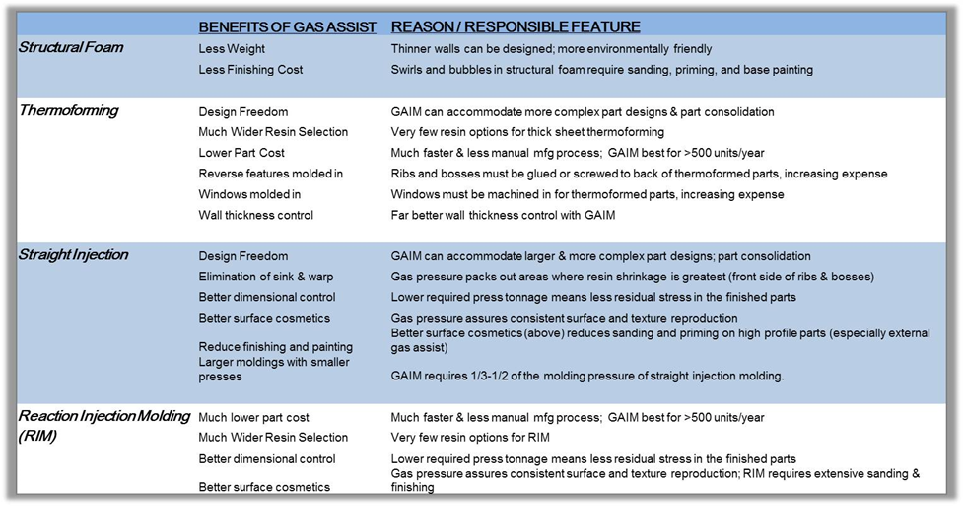
Mold Process Type | Internal Gas Assisted Injection Molding External Gas Assisted Injection Molding |
---|---|
Materials | ABS ABS/Polycarbonate Blends HIPS PBT Polyamide (Nylon) Polycarbonate Polyethylene Polypropylene PPA (Zytel) PPE |
Clamping Force | 85 to 1500 Tons |
Shot Size | 5 to 291 oz. |
Part Length | 10″ to 80″ |
Part Width | 10″ to 70″ |
Intended Application | Enclosures Covers Doors Equipment Cabinets |
Additional Molding Capabilities | Overmolding In-Mold Assembly Traditional Injection Molding Structural Foam Molding |
Additional Services | Finish Machining Painting Pad Printing Heat Staking Sonic Welding Assembly Packaging Design Engineering |
Testing & Inspection | CMM Dimensional Inspection Color Spectrophotometer Gloss Meter |
Lead Time | Quoted on job by job basis |
Production Volume | 200 – 5,000 Parts Typical Small to Medium Size Production Runs |