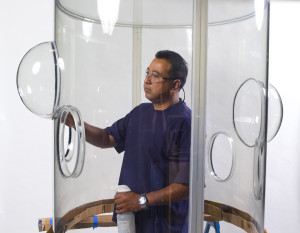
Plastic Fabrication Process:
Plastic fabrication is a very simple process where flat sheet of plastic is bent or bonded into a new form (similar to sheet metal bending) but with the many additional benefits of plastic, such as molded-in color or optical clarity, corrosion resistance, or electrical insulation. Sheet plastic can be bought in hundreds of different colors and textures, and the final product is only limited by the designer’s imagination. A wide variety of material options exist to meet cosmetic needs (color, texture, gloss or finish) or functional requirements (rigidity, flame retardant, impact strength, chemical resistance). Universal Plastics will share our expertise in thermoplastics to help you to find the right material for your part.
The equipment used in fabricated products include CNC and 5 axis routing machines to cut the plastic to size. We also have modular designed specialty machines for line bending used in combination with job-specific fixtures for bending and bonding/assembly. In addition, we provide many value-added operations such as drilling, bonded mounting blocks or custom foam shapes; installing threaded inserts; adding velcro fasteners and sewn webbing; and riveting components such as handles, hinges, latches and strikes, etc. In this way we can provide a more complete sub-assembly to meet your needs and reduce your in-house workload.
Advantages:
- Low upfront cost of tooling
- Highly cost effective for low to moderate quantities (300 – 5,000)
- Rapid prototyping and quick time to market
- Cosmetic benefits of plastic sheet: colors, textures, clarity, etc.
- Functional benefits of plastic sheet: rigidity, chemical resistance, flame retardant, impact resistance, etc.
- Ability to form very large parts
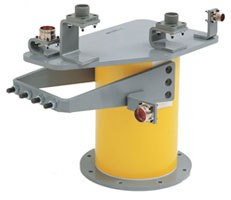
Applications:
Universal Plastics’ expertise in the application of plastic fabrication ranges across various industries and product types. Common applications include:
- Machine guards
- Displays
- Safety covers
- Plastic enclosures
- Structural bezels
- Radomes
- Equipment panels
For assistance with your design, just let us know. Our world-class engineering team will be happy to work with you to design a fabricated part for your specific application. To discuss how Universal Plastics can meet your plastic fabrication needs, please contact us.
Plastic Fabrication Capabilities at Universal Plastics:
Universal Plastics is the largest precision heavy gauge custom thermoformer in the Northeastern US with an asset base of 22 pressure formers, 14 vacuum formers and 26 5-axis trimming machines, supplying our customers with vacuum forming, pressure forming, including twin sheet forming and complex assemblies, with part sizes up to 12’ x 9’. In addition, we offer in-house tooling, an experienced engineering staff, and a full complement of secondary/finishing services, including our new state of the art paint booths which can produce automotive quality finishes. With a range of rotary formers, rapid manufacturing processes, and a global supply chain, we can produce thermoformed parts at the most competitive prices.
In addition to custom thermoforming, Universal Plastics also offers injection molding (including gas assist and structural foam molding) and custom blow molding. We would be glad to talk with you about the optimal process for your needs.
Contact us to discuss how we can meet your plastic fabrication needs.