APPLICATIONS: Vacuum formed parts are single component parts that come out of the vacuum forming process as the actual product or a substantial part of the finished product. These are enclosures or housings that are often replacements for sheet metal or fiberglass that need to be light but durable and have good strength relative to weight.
CAPABILITIES: Vacuum forming is a one-sided process. The finished part will have shape and detail on one side. The advantages to vacuum forming are less expensive tooling, faster turn-around and easier, less expensive updates and modifications compared to injection molding.
Thermoformed (or vacuum formed, as it is also known) plastic is THE state-of-the-art process for producing panels, covers, bezels and housings that are attractive and durable — yet lightweight and affordable.
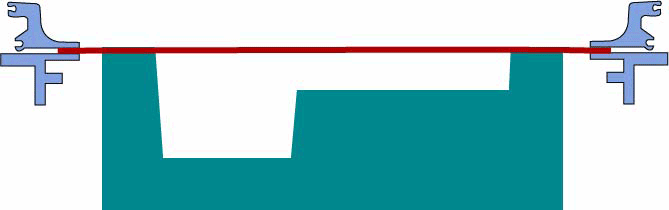
Attractive: Thermoformed plastic parts can be produced in a nearly unlimited variety of base materials, finishes, colors and textures.
Molded-In Styling Features: Logos, model designations, and other text and images can be formed right into the surface of the part. This eliminates the time and labor of adding these features, and they are a permanent feature of the part.
Durable yet Flexible: No material is more resilient than the thermoplastic resins that are available today. A vacuum formed part will not rust, it will not rot, it will not chip, and it can withstand considerable impact and return to its original shape!
Lightweight: Thermoformed plastic parts can be made from loll, density plastic with very thin walls to create a strong and durable, yet relatively lightweight part. Thermoformed plastic is considerably lighter—yet as stronger or even stronger—than molded fiberglass or sheet metal.
Less Expensive Than Other Processes: Compared to sheet metal or handlayed fiberglass, thermoformed plastic parts can be much cheaper. And tooling for thermoforming is many times less expensive than tooling for other plastic processes, such as injection, rotational or blow molding.
Fast Time-to-Market: Tooling for thermoformed parts can be designed, engineered and fabricated in weeks, putting thermoformed parts into the assembly stream much faster than other processes.
Design Flexibility: The tooling used to thermoform parts can quickly and economically be modified to create different versions of a part for different configurations of a basic product.
Seamless: Thermoformed parts, panels and housings are elegantly simple, consisting of a single, seamless sheet of plastic formed to the exact dimensions, color, finish and texture needed by the OEM.
Thermoformed plastic is the logical upgrade from sheet metal or fiberglass when parts, panels, housings and enclosures are needed that must be durable and attractive, yet lightweight and affordable.
Upgrade from Sheet Metal: Manufacturers using sheet metal for product housings can affordably upgrade to thermoformed plastic to create a more contemporary exterior for their product.
Upgrade from Molded Fiberglass: Products with fiberglass exteriors can be significantly reduced in weight and cost by upgrading to thermoformed plastic.
Bezels and Fronts: Housings for CRTs, touch screens or liquid crystal, flat panel or plasma displays are excellent candidates for thermoformed plastic.
Consoles and Instrument Panels: A panel that requires precise openings for gauges and controls, but also needs to be attractive and rugged, can be cost-effectively produced via thermoforming.
Three-Dimensional Housings and Enclosures: Exteriors of business machines, office equipment, medical and diagnostic units, electrical and electronic devices, and other consumer and commercial products are excellent applications for thermoformed plastic.
Doors, Hatches, Covers and Movable Panels: Panels that face the user, and need to be durable and attractive, are ideal candidates for thermoforming. They can be affordably produced with indentations and cutouts for hinges, latches, handles, brackets and other hardware.
Panels with Undercuts and Returns: Parts with edges that turn under, or panels with sections that wrap back, can be produced through an advanced the process called “pressure forming”.
Twin-Wall Panels: When a double-walled panel is needed, it can be produced in a single, affordable process via what’s known as “twin-sheet thermoforming”.
Wide Range of Colors and Finishes: Parts can be thermoformed with an inherent color in the resin, or the formed part can be painted and/or screen printed, and the surface can be hot stamped or given other finishes.
EMI/RFI Shielding: For electrical or electronic equipment that require housings with EMI and/or RFI shielding, it can be applied to required specifications in a secondary operation.
Insulation: Thermal or acoustic insulation can be affordably applied to the backside of a thermoformed part.
Thermoforming (or vacuum forming) is the process of heating a two-dimensional sheet of plastic, vacuum drawing it into a mold, and giving it an entirely new, permanent, three-dimensional form.
The entire process has six steps.
1. Create a Mold and Tooling: A mold is designed and fabricated along with secondary fixturing to support the thermoforming process.
2. Heat the Flat Sheet of Plastic: A flat sheet of resin is clamped into a frame, rotated into a heating chamber and heated to a pre-determined optimal temperature (Figure 1-Top).
3. Drape the Hot Sheet of Plastic Over or Into a Mold: The pliable, heated sheet of plastic is then either draped into a female mold or over a male mold, and tiny vacuum lines in the mold draw out the air between the plastic and the mold, while normal atmospheric pressure pushes the softened plastic against the mold.
4. Remove the Formed Sheet of Plastic from the Mold: Once the sheet of plastic has taken on the shape of the mold, it is cooled and withdrawn from the mold, then removed from the clamp frame.
5. Trim the Part: There is often excess material around the edges of the part, and that material is routed or trimmed off. If any additional machined features are called for, they are trimmed out.
6. Finish the Part: The part may be painted, screen printed or hot-stamped, and assembly—such as the attachment of hardware, subassemblies, cabling or wiring, electrical or electronic components, or other parts—may be performed.
The soft, heated sheet of plastic is draped into a female mold. Vacuum lines built into the mold draw the air from between the plastic and the mold, drawing the plastic against the surface of the mold while atmospheric pressure pushes against the backside of the plastic.
Thermoformed Plastic | Molded Fiberglass | |
---|---|---|
Per-Part Cost | Many times less expensive than molded fiberglass! | Twice or more the cost of a comparable thermoformed plastic part! |
Durability of Part or Panel | Will not rot, chip or crack. Highly durable and resilient! | Chips and cracks, and deteriorates when subjected to the elements |
Strength-to- Weight Ratio | Very strong! Can support many times its own weight! | Relatively strong, but also very heavy and cumbersome |
Characteristics | Features on one side only | Features on one side only |
Integration Potential | Seamless integration with other materials and into any size product | Wall thickness and radii limitations |
Finish Options | Virtually unlimited in terms of color, texture and surface features | Wide color options, but limited texture or surface features |
Base Materials | Variety of resins creates finish, weight, durability and performance options | Just fiberglass |
Design and Engineering Assistance | Extensive assistance in design, engineering, mold making, tooling and final integration | Varies from supplier to supplier |
Post-Production Capabilities | Painting, screen printing, hot stamping, shielding, insulation, assembly and fulfillment | Painting, maybe assembly |
Thermoformed Plastic | Sheet Metal | |
---|---|---|
Per-Par Cost | As little as half the cost of sheet metal in reasonable quantities | More expensive than plastic! |
Durability of Part or Panel | Will not rust, and will take impact without denting. Highly resilient and durable! | Strong, hut easily dents and takes scratches, and may rust |
Strength-to- Weight Ratio | Can support many times its own weight! | Relatively strong, but also very heavy |
Part Characteristics | Features on one side | Features on one side, crimps and welds show on backside |
Integration Potential | Seamlessly integrates with other materials into any size product | Weight limits integration possibilities |
Finish Options | Virtually unlimited in terms of color, texture and surface features | Usually painted; other limited finish options |
Base Materials | Each resin creates different finish, weight, durability and performance options | Just metal, usually steel |
Design and Engineering Assistance | Extensive support including design, tooling, finish options and final integration | Varies from fabricator to fabricator |
Post-Production Capabilities | Painting, screen printing, hot stamping, shielding, insulation, assembly and fulfillment | Differs widely from fabricator to fabricator |
Thermoforming presents the ongoing challenge of stretching a flat sheet of resin over a larger, multi-dimensional surface.
To prevent thinning and to better distribute material over a larger surface, three vacuum forming production practices have evolved in recent years.
1. Drape Forming: This practice uses a male mold, and the heated sheet of plastic is draped over it. A combination of vacuum draw between the plastic and the mold, atmospheric pressure against the backside of the plastic, and gravity help to distribute the plastic more evenly across the larger dimension of the new thermoformed part.
2. Snapback Vacuum Forming: Almost the exact opposite of drape forming, in this practice the sheet of plastic is allowed to slowly stretch as it is heated and it softens. When the mold is dropped down from the top, vacuum lines draw (or snap) the hot sheet up against the mold, helping to more evenly distribute material.
3. Plug-Assist Thermoforming: When there is an especially large, new., third dimension (or depth-of-draw) to be covered, a large plug is used to physically push the stretched sheet of material into the recesses of the mold.
Plug Assist Forming: Positive air pressure pushes the heated sheet of plastic up, stretching it and expanding its surface area. The plug assist then drops down into the cavity of the mold as the air between the plastic and the mold is evacuated.
What Is a Draw Ratio?
Whenever a flat sheet is drawn over a contoured surface, the material is going to stretch. A contoured part has a surface area greater than that of a flat sheet of the same length and width. This difference in surface area is known as the “draw ratio”.
There are a number of formulae to express the draw ratios of different shaped objects, and the mathematical formulations for each of these are available from a number of sources. Here are the three most common .Part Dimensions
2H (L+W)
where
D = Nominal draw ratio
= Height of box or rectangle
= Length of box or rectangle
= Width of box or rectangle
Therefore, a formed box with the dimensions 6″ height by 10″ length 13‘ would have a draw ratio of
class=Section14> 2 (6) (10+10)
(1 Oxl 0) D = 2 Tr R 2
D = Nominal draw ratio
R = Radius of the cylinder
Where:
TrR2+TrDH
11 R2
D= Nominal Draw ratio R= Radius of the cylinder
ID= Diameter of the cylinder H = Height of the cylinder
While vacuum forming offers many benefits to the OEM seeking attractive and durable, yet lightweight and inexpensive parts, panels and enclosures, there are two advanced technologies that offer even greater possibilities.
Pressure Forming: For better surface detail and texture, and for parts with significant depth of draw or undercuts, pressure forming is the solution. Using vacuum pressure to draw material against the surface of the mold, pressure forming adds positive air pressure against the backside of the plastic to push the resin even more tightly against the surface of and into the recesses of the mold.
Twin-Sheet Thermoforming: This process forms two parallel sheets of plastic at the same time, then thermobonds them together to produce a double-walled panel.
Pressure Forming: Vacuum pressure draws the plastic against the mold with atmospheric pressure assisting the process. In pressure forming, however, both vacuum pressure and positive air pressure pull and push the heated resin even more tightly against the surface and into the recesses of the mold.
Two key considerations in the design and engineering of thermoformed parts are the radii of corners and draft angles.
Tight radii should be avoided, as they can create weak areas where the finished part may crack. On female cavities, however, the radii should vary with depth.
2-Inch Depth: Approximate radii = .030″ minimum
6-Inch Depth: Approximate radii = .075″ minimum
12-Inch Depth: Approximate radii = .150″ minimum
Other Values May Be Interpolated
Variations in Part Thickness: This occurs for many of the reasons just given. Variations in thickness are most often caused by multiple or secondary draw ratios within the part (Figure 13). it may be necessary to design around theses problems, but if forming techniques alone do not solve them, secondary assembly measures may be necessary. To accommodate load-bearing requirements or stiffening needs, it is possible to bond spacer blocks, fastening bosses with inserts, or reinforcing blocks to the backside of the part. However, because the backside wall will probably not be uniform (Figure 14), tolerances based on individual parts must be established. Design some latitude into the part, and discuss with Universal Plastics’ engineering staff if gluing secondary pieces to the backside of the part is practical and makes sense.
Material: In determining the best material for the application, there are two major considerations.
Will It Provide the Physical Characteristics Needed in the End Product? After it’s been pressure formed, what appearance, texture, rigidity and color will the plastic have?
Can It Be Pressure Formed? How will pressure forming change any of the material’s characteristics?
Required Characteristics: These include impact strength, resistance to chemicals and solvents, paintability, weatherability, stability, heat deflection, creep and stiffness. The material must also provide hot strength and flow characteristics to create a structurally functional part that is cosmetically appealing and able to accept detail.
Interim Tooling: To provide prototype parts, it may be feasible to use renvvood, urethane board or non-water-cooled epoxy molds. The resulting parts will not cosmetically resemble the finished product, but they can be used to test the design and help develop the forming techniques required. Also, it is relatively easy—and not too expensive—to modify a renwood, urethane board or epoxy mold.
Variations in wall thickness are most often caused by a secondary draw in the design of the part.
It is not likely that the backside of the wall of this part will be uniform, and that has to be factored into the design and engineering of the part.
The single most important factor in producing quality thermoformed parts is the tooling used to form the parts!
Aluminum Tooling: To make consistent, cosmetically appealing parts, there is no substitute for machined aluminum or cast aluminum temperature-controlled tooling. They both provide good temperature control, and they both produce parts with minimal warpage, and aluminum tooling-produced parts are dimensionally more consistent and stable.
Cast Aluminum: This alternative can be less expensive than fabricated molds when producing larger-sized tooling. However, its tendency towards porosity limits the texture choices.
Machined Aluminum: A temperature-controlled mold machined from a block of aluminum is clearly the superior alternative for quality pressure forming. Tolerances can be held to industry standards, and plates can often be milled and laid up with .005-inch vacuum openings along a detail area to evacuate air.
More detail can be achieved and texture definition can be improved because porosity is eliminated.
Epoxy: These molds are formed from an epoxy resin that is poured into a reverse mold. It hardens to form very affordable tooling, but epoxy molds are only recommended to producing pre-production samples or very short production runs.
Tooling Design Considerations: Such factors as drafts, undercuts, corner radii, cutouts, holes and slots need to be considered when designing tooling. Female molds do not theoretically need any draft other than for cast removal in producing the mold. In actuality, however, enough draft is needed to prevent the texturing from abrading Nvh en the thermoformed part is removed from the mold. The amount of draft needed is determined by the depth of texture. For example, if the texture of the tool has a depth of .003-inch, the amount of draft needs to be 1.5 degrees for each .001-inch of depth. (3 x 1.5 = 4.5 degrees of draft per side). This allows for proper part removal from the tooling.
Successful thermoforming of a quality part, panel or component requires some of the most sophisticated equipment in the plastics industry.
Many factors need to be considered when selecting the equipment that will configure a comprehensive, efficient and effective pressure forming system.
Top and Bottom Platens: These should have clamping pressures of 10,000 pounds or more so they are held together when pressure is being applied to the thermoformed part.
Top Screening Heating Elements: These should have zone control or a way of screening heat locally.
Air Flow System: Only the correct amount of airflow will cool the thermoformed part at the optimal rate, and airflow has to be adjustable based on the ambient temperature and humidity.
Cycling Systems: These must be able to repeat each step in the thermoforming process with accuracy to + a few seconds.
Secondary Operations: The machinery used for secondary operations is just as important as the tooling and vacuum-forming equipment. The quality and precision of trimming and routing fixtures will have a direct impact on the quality and consistency of the finished part. With proper planning, many of the trimming functions can be designed into the mold, minimizing secondary operations. Also, the advent of robotics creates another avenue of consistency toward producing uniform parts with close tolerances.
Post-Thermoforming Operations: Once the part has been formed and trimmed and/or routed, numerous other procedures may be needed to prepare the part for integration into the final product.
Painting: The part may need to be painted, and Universal has in-house painting capabilities, that will reduce the overall part cost and take time out of the manufacturing process.
Screen Printing and Hot Stamping: As with painting, Universal can screen print or hot stamp logos, company identification, model designations, warning labels of other indicia onto the part, both money and time are saved.
Assembly and Fabrication: If latches, hinges, handles, brackets, supports, harnesses or any other hardware or electronics are to be attached to the vacuum-formed part, having the thermoforrner perform these procedures reduces the number or vendors, minimizes trans-shipping of the part, reduces costs and saves time.
Fulfillment: Universal can package and ship the part—or even the completed product—to a contract manufacturer, the final assembly point, a reseller or the actual end-user of the product!
When is the time right to make the upgrade from molded fiberglass to thermoformed plastic? There are several factors to consider.
When to Stay with Fiberglass: Products that are going to be produced in relatively small numbers, or products that are very likely to undergo significant design changes, might be better served with molded fiberglass
Less than SOO Units over the Life of the Product: Thermoforming a part requires in investment in tooling, so if total units that will be produced is not likely to exceed 500, and durability and lightweight are not serious considerations, staying with molded fiberglass makes sense.
Significant Design Changes Are Planned: If the product is in an experimental state, and it is likely that significant changes will be made that will affect the shape, size and design of its enclosure, it may not be wise to invest in tooling for a thermoformed housing.
When to Take a Serious Look at Thermoformed Plastic: If lifetime production of the unit is likely to exceed 500 units, or the benefits of thermoformed plastic are important to the success of the product, an investment in thermoforming begins to make sense.
More than 500 Units over the Life of the Product: Once it appears that production of the product will reach 500 units, making an investment in thermoformed plastic makes sense, as the investment in tooling will pay for itself in a significantly reduced per-part cost.
Appearance Is a Critical Factor: If the appearance of the product is important to the success of the product in the marketplace, no material produces a more attractive and contemporary housing or exterior than thermoformed plastic. An investment in a thermoformed housing will easily pay for itself in increased unit sales of the product.
Performance of the Housing or Exterior Is Important: If the exterior of the product needs to be durable and resilient, or lightweight, or not subject to rotting or rusting, thermoformed plastic is a must.
When to Make the Upgrade to Thermoformed Plastic: For many OEMs using molded fiberglass, the time has arrived to make the upgrade.
Over 1,000 Units: If over 1,000 units will be produced, the reduced per-part cost of thermoformed plastic will pay for the tooling investment many times over!
Per-Part Cost Is Critical: If competitive pressure makes it necessary to reduce costs wherever possible, shifting to thermoformed plastic will dramatically reduce the per-part cost over molded fiberglass by 5096 or more!
There are also distinct points at which it makes sense to upgrade from sheet metal to thermoformed plastic.
Benefits of Sheet Metal: When very small numbers of enclosures or components are needed quickly, sheet metal—which requires no tooling—is affordable and practical.
Less than 100 Units over the Life of the Product: If a very small number of total units will be produced, an investment in thermoforming tooling may not make sense.
The Product Will Go through Several Iterations: If the product is being developed in stages, and limited numbers of units are needed for beta testing, for example, sheet metal is quick and affordable
Appearance and Durability Are Not a Factor: If the appearance of the product’s housing is of no real importance, and having an enclosure that’s durable and attractive is not important, staying with sheet metal also makes sense.
When Sheet Metal Becomes Cost-Effective: It does not take too long for the relative benefits of thermoformed plastic over sheet metal to become apparent.
More than 100 Units Will Be Produced: The considerably lower per-unit cost of a thermoformed part against that of a comparable sheet metal part means that an investment in thermoforming tooling will begin to pay for itself once total production approaches 100 units.
Contemporary Design Is Important: Sheet metal can only be formed into essentially flat planes with minimal stylization. If the product needs a state-of-the-art exterior, sheet metal is just not an option.
Durability and Performance Are Critical: Unless the sheet metal component is fabricated from stainless steel, it will begin to rust almost immediately. Sheet metal also picks up scratches and dents, which thermoformed plastic will not.
When Sheet Metal Is Really Not an Option: For any product produced in reasonable quantities, upgrading from sheet metal to thermoformed plastic is an easy decision.
Over 500 Units: The breakeven of tooling against reduced per-cut cost from sheet metal to thermoformed plastic is around 100 units. For a product that will be produced in the hundreds, the savings by upgrading to thermoformed plastic is significant!
Costs Must Be Reduced! The dramatic savings that vacuum-formed parts represents makes the upgrade to thermoformed plastic from sheet metal one of the first consideration when it’s time to cost-down a product.
An examination of the use and application of the part to be vacuum formed will result in better planning, and a better quality part.
Increased Tolerances: Thermoforming requires tolerancing that is different than machined dimensions of secondary operations performed after the forming process. Molded tolerances should be +.020 for the first inch, and +.001 for each additional inch. The shrink rate tolerance for thermoformed plastic is typically +.001/inch.
Design Limitations: The thermoforming process is somewhat unique, so an understanding of its design limitations can help both the thermoformer and the end user get greater satisfaction from the product.
There are three major considerations when designing thermoformed parts.
Satisfying the End User: Will the component be affordable, attractive, durable and easy to integrate into the finished product?
Material to Be Used: Will the plastic come out of the process with the right finish, texture, features, dimensions, rigidity and durability?
Tooling and Equipment Selection: Will the tooling and thermoforming equipment lead to a process that is efficient, repeatable, consistent, and labor and material-efficient?
Questions? What makes the product marketable? What alternative design features can accommodate the process? Will the part function? There are several end-use issues that need to be considered.
Heat Deflection: Does the resin have a high enough heat deflection threshold for the operating temperature of the unit?
Thermal Expansion: How might expansion of the part when exposed to heat affect the final assembly?
Cosmetics: How important are the aesthetics of the finished part?
Variations in Thickness: How thin or thick can different areas of the part be?
Properties and Formability: How will the resin’s characteristics change after it has been thermoformed?
Load-Bearing: Will the part need to bear weight?
Agency Requirements: Does it need to meet UL, CSA, FDA or NSF standards?
Allow for Expansion: A resin’s thermal expansion doesn’t change after expansion varies from resin to resin. Parts must be designed so they can expand, or flexural points must be built into them so they will not fatigue and they can accommodate expansion and contraction.
Solid Model Geometry: In most cases, the designs used for the sheet metal or fiberglass part can be converted into the three-dimensional designs needed for thermoforming.
Purchasers of thermoformed parts and components need to be involved in the design and engineering of the part, as well as the tooling and equipment required to produce it. However, it is the thermoformer that is selected to produce the part that is ultimately responsible for producing parts that are affordable and consistent, meet spec, and are delivered on time.
What to Look for in a Thermoformer
Several factors should be considered in the process of selecting a thermoformer.
In-House Engineering: Universal has its own engineering staff and can provide relevant, practical, ongoing expertise to the design and engineering process.
In-House Tooling: Universal can design and produce tooling in house and offers faster turnaround on tooling, lower costs for tooling, and complete quality control through the entire design, engineering, production and post-production continuum.
ISO Registration: Universal is ISO registered. Quality is not just a buzzword in their advertising program.
UL-listed Fabricator: If fabrication will be required, a UL-listed fabricator will insure adherence to all UL standards and guidelines.
Professional Affiliations and Recognition: Universal is active in industry associations and societies such as the SPI and SPE, and has been recognized by the industry for its innovation and excellence?
In-House Post Thermoforming Capabilities: Universal in-house trimming, routing, painting, screen printing, assembly, fabrication and fulfillment capabilities makes it possible able to produce a quality thermoformed part more affordably and more quickly. While some thermoforrners advertise they can paint parts, they really have subcontractors that do painting for them. Sending parts to a subcontractor adds overhead to the cost and time to the process.
Industry Experience: Universal has produced parts for other manufacturers in many industries and has an understanding of the nuances and peculiarities of those industries that are invaluable.
Seek a Partnership: Universal forming a part—or several parts—is far more than a supplier. Universal is your partner, and the success of your finished product will be the result of the skill set, capabilities and dedication to quality of both companies.